Praxisbeispiel
Erhöhung der Anlagenverfügbarkeit
Durch systematische Methodik und Tool-Unterstützung erreichten wir durch eine Digitalisierung von analogen Daten eine nachhaltige Erhöhung der Verfügbarkeit von Maschinen und Anlagen, die bisher nicht digital an das Unternehmens-Netzwerk angeschlossen waren.
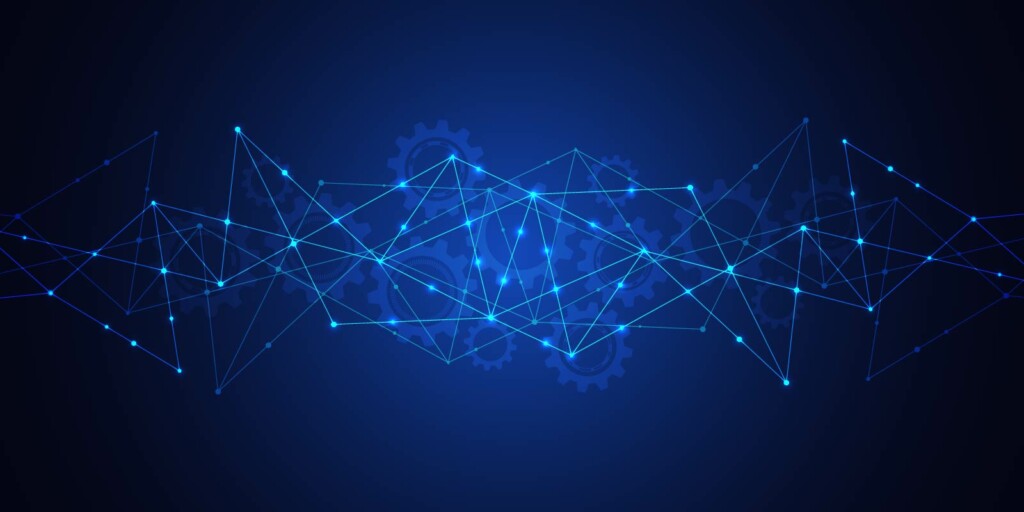
Hintergrund
Nach einer langen Insolvenz und einem Eigentümerwechsel stand unser Kunde – eine der größten Sandgießereien in Europa – vor massiven organisatorischen, prozessualen und technologischen Herausforderungen. Die strategische Neuausrichtung der Firma galt im ersten Jahr der Übernahme im Wesentlichen der Stabilisierung des Geschäftsbetriebes und damit der Produktion. Ein betagter Maschinenpark mit mangelhafter analoger Datenerhebung (Auftragsdaten, Kennzahlen, Fehlzeiten, Verlustursachen etc.) und fehlendem Optimierungsprozess (KVP) machte es zwingend nötig, so schnell wie möglich Transparenz über die Produktionsdaten und Hoheit über deren Analyse zu erlangen.
Konkrete Aufgabenstellung
- Herstellung der Transparenz über Anlagendaten, Produktionskennzahlen und Verlustarten der Gesamtanlageneffektivität (OEE) Organisatorik, Technik und Qualität.
- Erhöhung der OEE über die Reduzierung organisatorischer Verluste durch Optimierung der Produktionsorganisation.
- Erhöhung der OEE über die Reduzierung technischer und qualitativer Verluste durch zielgerichtete Optimierung von Maschinen, Werkzeugen und Vorrichtungen sowie einen wirksamen Fehler-Management-Prozess.
- Erhöhung der Effizienz in der Produktionssteuerung und den Produktionsprozessen.
- Stabilisierung und Erhöhung der Anlagenverfügbarkeit mit dem Ziel, Liefer-Rückstände abzubauen.
KBC-Lösungsansatz
Unser erster Schritt war die Herstellung der Transparenz über auftretende Verlustarten an Maschinen, Werkzeugen und Vorrichtungen inklusive deren technische Zustände (Schäden, Leistungsdefizite und Wartungsstau). Dazu wurden auch die real gelebten Prozesse auf dem Shop Floor aufgenommen.
Der zweite Schritt nennt sich „Digitalisierung analoger Daten“. Situativ wird hier je potenzieller Datenquelle (z.B. eine Maschine) entschieden, wie bisher nicht vorhandene oder verwertbare Daten, einheitlich manuell erfasst und konsolidiert werden können. Dabei kann es sich in diesem Schritt um manuelle (analoge) oder bisher nicht vernetze digitale Daten handeln. Hierzu wurden Schicht- und Auftragsprotokolle soweit wie möglich standardisiert und automatisiert. Nach umfangreicher Schulung des Produktionspersonals wurden die Erfassungsaktivitäten begleitet, um schnellstmöglich Datentransparenz herzustellen.
Der dritte Schritt beinhaltete die Datenanalyse im KBC Produktions-Monitor (eine Excel/ VBA-basierte Datenbank), der unmittelbar und universell in Unternehmen einsetzbar ist. Durch die gewonnene Transparenz und Details der Verluste (im Sinne der OEE) konnte das Projektteam sehr schnell Prioritäten für die anschließenden Optimierungsaktivitäten ableiten. Die begrenzten personellen und finanziellen Kapazitäten wurden somit sehr fokussiert mit der Ursachenanalyse, Maßnahmendefinition und -umsetzung eingesetzt. Aufgrund der hohen Datenqualität konnten auch verdeckte Zusammenhänge, wie zum Beispiel zwischen Produktqualität und dem Einsatz von Werkzeugen in bestimmten Schichten oder Auftreten bestimmter Verlustarten bei der Produktion einzelner Produkte, aufgedeckt werden.
Erzielte Wirkung
Mit unserem Lösungsansatz und der dabei gewonnenen Transparenz durch die „Digitalisierung analoger Daten“ war es innerhalb kürzester Zeit möglich, die OEE signifikant zu steigern (teilweise über 20%) und die Produktion damit zu stabilisieren. Unser Kunde realisierte damit nicht nur eine erhöhte Anlagenverfügbarkeit, sondern schaffte sich auch den nötigen Freiraum, Leistungsdefizite und Wartungsstau bei Maschinen proaktiv abzuarbeiten.
Des Weiteren war die Grundlage für den vierten Schritt geschaffen: Effizienz in der Datenerhebung. Durch den Einsatz einer KBC „IoT-Box“, kann eine analog Datenerfassung an Maschinen und Anlagen innerhalb von Tagen nachträglich und unabhängig von der jeweiligen IT-Infrastruktur in eine autarke digitale Erfassung umgewandelt werden – ein wirksamer Baustein für eine effektive und effiziente Digitalisierung und Vernetzung von Produktionsdaten.