Fachartikel
Produktrückrufe: Sonderfall Hochvoltspeicher in Elektrofahrzeugen
Produktrückrufe gehören leider zum Unternehmensalltag – sei es wegen Qualitätsmängeln, Sicherheitsbedenken oder Rechtsverstößen. Dabei handelt es sich nicht etwa um ein branchenspezifisches Phänomen, im Gegenteil: Sie betreffen die Automobilindustrie ebenso wie den Maschinen- und Anlagenbau, die Unterhaltungselektronik oder die Lebensmittelindustrie. Was alle Branchen gemeinsam haben, sind die Herausforderungen, rechtliche Folgen sowie hohe Kosten und Imageschäden die so eine Rückrufaktion mit sich bringt.
Die Meldungen von Batterierückrufen von Elektrofahrzeugen häufen sich derzeit in den Medien. Diese sind deutlich komplexer als herkömmliche Produktrückrufe. Neben den erhöhten Sicherheitsanforderungen beim Rückruf kommen spezielle regulatorische Vorgaben zur Rücknahme und Entsorgung hinzu. Unternehmen müssen daher ein besonders sorgfältiges und umfassendes Rückrufmanagement etablieren, um alle Aspekte abzudecken.
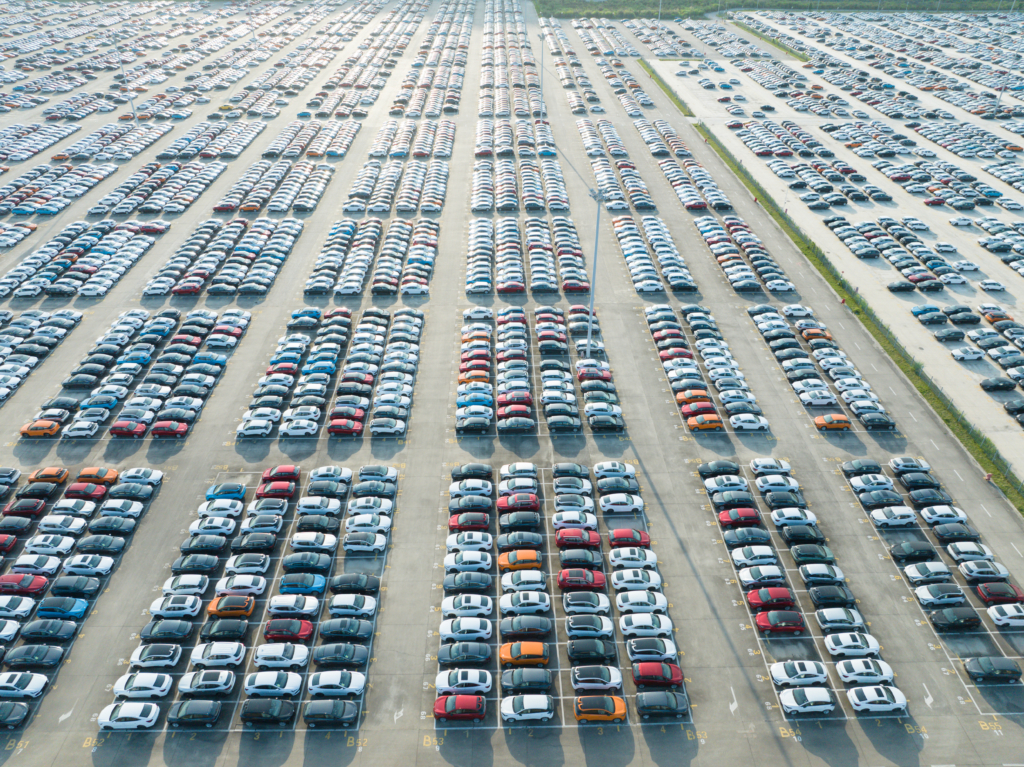
Produktrückrufe verhindern
Damit es erst gar nicht so weit kommt, gilt es, bereits im Vorfeld Präventivmaßnahmen zu ergreifen, um Produktrückrufe möglichst zu verhindern. Hier kann es hilfreich sein, die notwendigen Rollen, Strukturen und Prozesse zu etablieren, die im Falle eines Rückrufs erforderlich sind. Dabei ist die Fehlerrückverortung, d.h. die Rückverfolgung der Ursachen bis in die Kernprozesse die Basis für nachhaltige Maßnahmen zur Fehlervermeidung für zukünftige Produktgenerationen.
Es ist wichtig, vorab Standards zu definieren, nach denen Produkte entwickelt, gefertigt und geprüft werden. So lassen sich technische Ursachen für Mängel von Anfang an minimieren. Gleichzeitig muss Transparenz in der Lieferkette herrschen, damit Probleme frühzeitig erkannt werden können. Regelmäßig durchgeführte Requalifikationen von Lieferanten können dabei helfen, nachhaltig die Fehlerfreiheit und Qualität der Komponenten sicherzustellen. Entscheidend ist auch eine systematische Analyse von Felddaten. Durch die Auswertung von Reparaturberichten, Kundenreklamationen und anderen Informationen aus dem Markt, lassen sich kritische Produktschwachstellen identifizieren, bevor sie zu Rückrufen führen.
Auswirkungen durch Rückrufe minimieren
Droht eine Rückrufaktion, gibt es Möglichkeiten, die Auswirkungen eines Produktrückrufs abzumildern. Ein wichtiger Hebel ist die Optimierung der Reparaturprozesse. Durch eine schlanke und effiziente Abwicklung lassen sich die direkten Kosten für Rückholung, Lagerung und Entsorgung der betroffenen Produkte deutlich reduzieren. Gleichzeitig kann eine Anpassung der Teilepreise die Einstandskosten senken.
Darüber hinaus ist es sinnvoll, den Umfang eines potentiellen Rückrufs jederzeit abschätzen zu können. Durch eine erhöhte Rückverfolgbarkeit und lückenlose Überwachung der Lieferkette können Unternehmen genau bestimmen, welche Produkte oder Chargen tatsächlich betroffen sind, um so die potentielle Rückrufmenge zu quantifizieren. Gleichzeitig müssen betroffene Betriebe eine kontinuierliche Kommunikation mit Behörden sicherstellen, um Bußgelder und andere rechtliche Konsequenzen zu minimieren.
Produktrückrufe kontrollieren
Ist der Ernstfall bereits eingetreten, kommt es darauf an, den gesamten Rückrufprozess bestmöglich zu steuern. Die systematische Dokumentation aller Maßnahmen und Bedarfstransparenz zu schaffen, ist dabei essentiell. Hier gilt: Je präziser das Risiko bewertet, desto detaillierter kann die zurückzurufende Menge bestimmt werden. Die sogenannte Rückrufpopulation ist u.a. abhängig von der Länge der Lieferkette sowie der Tiefe der Produktion. Sind die betroffenen Kunden bestimmt, lässt sich das geographische Ausmaß ermitteln und die entstehenden Kosten abschätzen.
Um den Herausforderungen eines Rückrufs effizient zu begegnen, sollten die Leistungsfähigkeit der Lieferanten, deren Produktionskapazitäten sowie der Reparaturstatus stetig überwacht werden. Einerseits, um Potenziale nutzen zu können und andererseits drohende Engpässe oder Ausfälle frühzeitig zu erkennen und Gegenmaßnahmen einzuleiten. Denn: die Versorgungssicherheit für die Rückrufaktion hat oberste Priorität.
Eine erfolgreiche Rückrufaktion setzt außerdem eine strategisch gut geplante, zielgerichtete Kommunikationskampagne sowie ein im Detail geplantes Retourenmanagement voraus. Für betroffene Kunden ist ein Rückruf stets mit Unannehmlichkeiten verbunden, für die der Hersteller verantwortlich gemacht wird. Daher sollten Entschädigungs- und Kundenbindungsmaßnahmen ergriffen werden, um der Unzufriedenheit von Kunden und nachhaltigen Imageschäden entgegenzuwirken.
Sonderfall Batterierückruf von Elektrofahrzeugen
Batterierückrufe erfordern ein deutlich komplexeres und aufwendigeres Management als herkömmliche Produktrückrufe. Neben logistischen Herausforderungen, besonders von defekten oder beschädigten Hochvoltspeichern und regulatorischen Anforderungen ist ihre Komplexität ein weiterer Aspekt: Hochvoltspeicher sind hochintegrierte Bauteile, bei deren Entwicklung der Fokus heute überwiegend auf Energiedichte und Gewicht liegt – und nicht auf Austauschbarkeit von defekten Bauteilen. Als Herzstück und zugleich kostspieligstem Bestandteil, entfallen bis zu 60 Prozent der Herstellungskosten auf die Hochvoltspeicher in Elektrofahrzeugen. Die gängige Praxis, diese wertvollen Komponenten bei Defekten, Schäden oder auch Leistungsabfall zu verschrotten, steht zunehmend in der Kritik und treibt die Kosten eines Produktrückrufs noch weiter in die Höhe. Sind zusätzlich mehrere Baureihen oder Marken von dem Defekt betroffen, kann ein Batterierückruf in die Milliarden gehen.
Ein theoretisches Rechenbeispiel dazu: Die durchschnittlichen Herstellkosten eines Elektrofahrzeugs liegen derzeit bei rund ca. 32.000 €, die darin enthaltene Batterie macht bei einer konservativen Annahme von 50% knapp 16.000 € aus. Die jüngsten Produktrückrufe, aufgrund von Defekten am Hochvoltspeicher beliefen sich weltweit auf bis zu 150.000 Fahrzeugen. Gehen wir davon aus, dass der Speicher aufgrund eines erheblichen Mangels oder Sicherheitsrisikos ausgetauscht werden muss, belaufen sich die Kosten dieses theoretischen Szenarios allein für den Hochvoltspeicher auf 2,4 Milliarden Euro, wobei die operativen Rückrufkosten, Kosten für Handling, Ein- und Ausbau, Entsorgung bzw. Recycling oder Instandsetzung der defekten Speicher und eventuelle Entschädigungen von Kunden noch nicht berücksichtigt sind.
Produktrückrufe sind für Unternehmen eine enorme Herausforderung und mitunter komplex. Daher ist es entscheidend, Rückrufe möglichst zu vermeiden und frühzeitig präventiv tätig zu werden. Tritt der Ernstfall ein, muss der gesamte Rückrufprozess präzise kontrolliert werden, besonders bei Elektrofahrzeugen mit ihren hochkomplexen und kostspieligen Hochvoltspeichern. Um bei Batterierückrufen extrem hohe Kosten zu vermeiden, sollten Hersteller zukünftig die Reparaturfähigkeit ihrer Speichersysteme noch stärker in den Fokus rücken. Denn die Nachhaltigkeit und Wirtschaftlichkeit der Elektromobilität hängt maßgeblich vom richtigen Umgang mit defekten Hochvoltspeichern ab.
Ein Beitrag zu diesem Thema ist auch online bei der Automobilwoche erschienen.