Publication
Preventive supply chain management
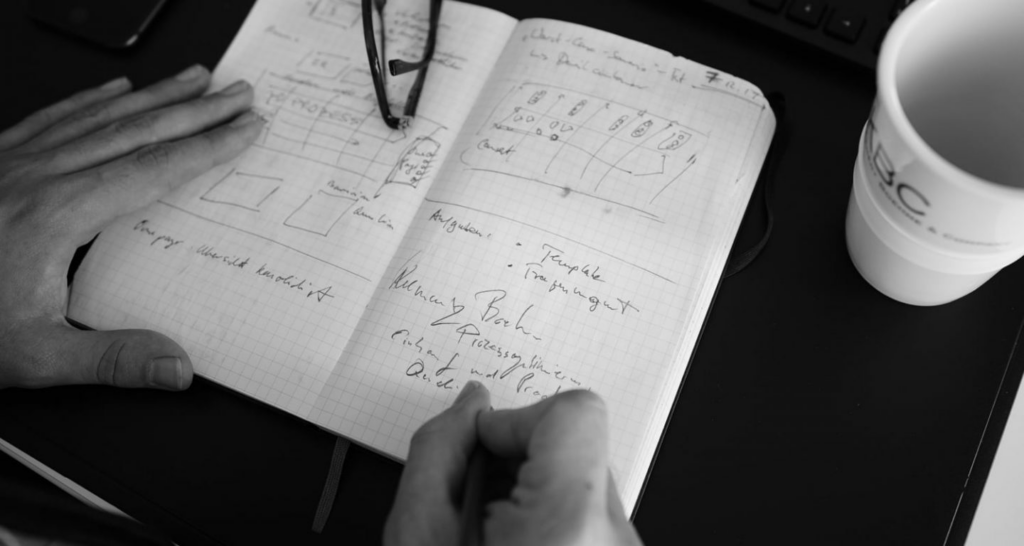
The unforeseeable exchange of diesel for petrol, monopolistic supplier markets in key technologies, uncertain political conditions in times of Brexit and the “customs dispute” of the USA as well as short-term interruptions in production – if you look at the news today, one thing can be deduced very quickly: the time left to manufacturers and their suppliers for (post-) industrialisation is getting increasingly shorter.
The role of purchasing
Through fixed product launches of new or revised products or late product changes from the development departments, the procurement department of industrial companies has always played the role of a “sandwich” position between development and production.
The electromobility is increasing
Disruptive events in the entire automotive industry, in particular the diesel scandal and the associated decline in demand for diesel engines by all manufacturers, are forcing OEMs to gradually shift their focus to electromobility. The Volkswagen Group has announced that it will launch 70 new e-models by 2028. An important role to achieve this goal is played by the industrialisation of new technologies (electric motors, battery storage, etc.), ensuring a robust supply chain, as well as compliance with new guidelines and laws.
The supplier himself is only one part of the risk factors
Due to the still strongly growing complexity of supply chains, their preventive control and integration is indispensable – from ensuring the transparency of component changes, continuous demand forecasting and the associated safeguarding of capacity, through to series process and product releases at the suppliers on site.
Preventive control is based on ensuring the transparency of component changes from development. By providing comprehensive information on the parts components, procurement is able to evaluate the effects on the supply chains (affordability, costs, duration) and, if necessary, initiate specific measures.
A continuous demand forecast along the supply chains enables suppliers to prepare for changes in demand and technology at an early stage. Only the earliest possible communication of the requirements (parts quantity, requirement period and requirement location) facilitates the procurement departments to effectively control the supply chain risks (e.g. supplier dependencies, etc.). In this case, robust and sustainable data management along the entire supply chain is essential.
The task of manufacturers
In addition, the direct securing of capacity at suppliers is another central component for the proactive avoidance of risk factors. New technologies and high investment costs are creating an increasing number of emerging monopolistic or duopolistic supplier markets (battery cells, catalysts manufacturers) It is therefore essential for industrial companies to identify critical component volumes as early as possible in order to guarantee a networked supply chain including secured capacities. In supplier markets, first come first serve is more important than ever.
When compared to his competition, the early application of the KBC approach to preventative supplier management enabled a premium OEM to significantly reduce the impact and consequences of the new WLTP and RDE test cycle, secure demand and capacity, and therefore prevent any slumps in sales. The manufacturer was able to produce all planned vehicles with the new technology.