Publication
Bottleneck management due to crisis situations
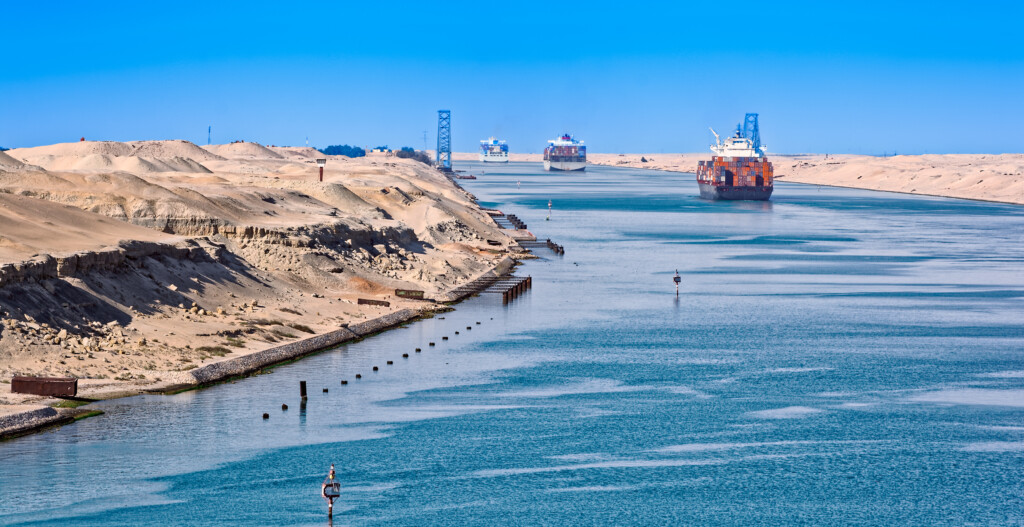
When supply is jeopardized by delivery bottlenecks
Manufacturing companies are continuously exposed to uninfluenceablen risks that can have an impact on their own supply situation. . This includes global Handelsbeziehungen and thus complex, closely timed supply chains or politically induced challenges, such as crises and wars, blockades of important transport routes or transshipment points, as well as border controls and customs controls. If such a risk becomes an actual problem, there is a risk of supply disruptions, production interruptions or high competitive pressure due to a shortage of resources. In addition, high inventory and storage costs may become necessary to cover a volatilen deliverysituation and increasing customer dissatisfaction due to poor delivery reliability gerufen. . Frequently, eincreased Memployee dissatisfaction due to permanent work in reactive mode (task force) is also the result.
In order to counteract these consequences in the event of a bottleneck , , fast and efficient management of the situation and the management of the associated challenges is necessary.
Challenges in congestion management
- In the case of bottleneck management, the rapid creation of transparency regarding the supply of production is crucial.
- The systems (ERP) at the companies , which are designed for regular use, are usually unable to map the actual supply situation.
- A reliable and up-to-date database is therefore the success factor for being able to react quickly to new bottlenecks every day.
- Suppliers generally have no information about the criticality of their customers’ requirements and are faced with a conflict of interest between several buyers.
Realizing fast and effective results in the event of a bottleneck by setting up and operating a supply cockpit
The following steps are necessary to implement a supply cockpit (dashboard):
Definition Objectives and derivation of data requirements
Before the actual dataprocurementung, the objectives to be pursued must be defined.Here introduce yourself u.a. the following questions: Which aggregations are necessary (part number vs. End product level)? Which value chain depth should be mapped? Which timeslicen shoulden be mapped (Kalender weeks, days, …)?
Procurement of usable data
The next step is to create transparency about the availablen and additionally requiredn data and systems. The data is validated and missing or implausible data ert.
Data preparation and modeling
This is followed by the data connection from heterogeneous sources and the introduction of potentially necessary aggregation levels such as timeslices and product level.
Dashboard and Metrics design
For the setup and operation of a supply cockpit for efficient control (program, delivery schedule, …) the data e.g.B. by filtering according to addressee-oriented criteria (markets, time slice, …).
Report and derivation of measures
The dashboard created is used and reported on at all hierarchical levels for reporting purposes to create transparency about the supply situation. In detail, a comparison of requirements and delivery capacities and quantities is carried out and components are prioritized with the involvement of the supplier.
Operationalization
In order to definethe processes and responsibilities wuring the bottleneck situation , it is advisable to visualizesieration using a process diagram. This can include work instructions, standards, templates, etc. help.
Success factors
In addition to the establishment of a supply cockpit , the consistency of the reporting system in the hierarchy and the support on site at the supplier are crucial. Only in this way can effective and feasible measures be derived as quickly as possible from a holistic view of the situation. In the event of a crisis, cooperation and close coordination between customer and the supplier is key.