Pressrelease
“The number of recalls will increase”
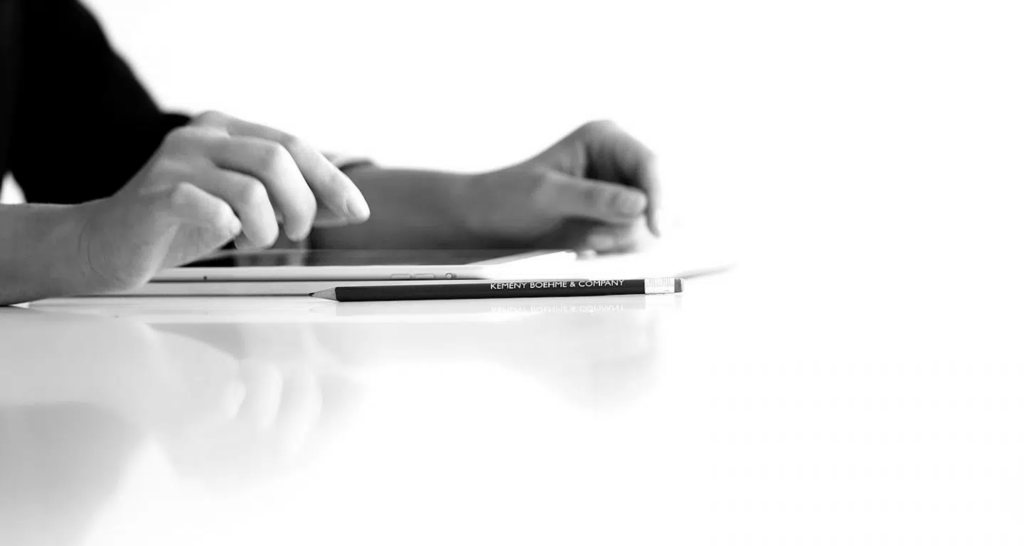
Georg Huber, Partner at the management consultancy Kemény Boehme & Company (KBC), explains why the number of recalls will continue to increase and how manufacturers could reverse the trend.
Munich, 14 July 2016 – Excessive Diesel emission values, defective ignitions and problematic airbags are increasingly in the public limelight. But have we already reached the peak of recalls? According to our estimate as management consultants specialised in technology and automotive companies, we will have to negate that.
One reason being: Past cases like Diesel manipulations have sensitised the authorities and consumers considerably and have therefore placed vehicle manufacturers and suppliers into the central focus of critical reviews. Manufacturers are therefore forced to react to even the slightest issues relevant to safety or legislation so as not to risk being suspected of keeping well-known risks under wraps. Any forthcoming statutory amendments and the personal liability risk of management will also aggravate the situation further. This is why we firmly believe that recalls will only increase in the next few years.
The levers of recall prevention
There are, however, effective recall prevention strategies available. With Supplier Management being one aspect. Global value-adding chains, highly fluctuating utilisation and cost pressure are only a few of the causes for possible sources of error along the supply chain. From the definition of specifications all the way to process monitoring in serial production, this is where we can find considerable optimisation levers. In this regard, transparency and consistency play an important role, as do feasible safeguarding mechanisms applied to prevent fluctuations in product quality. Suppliers, however, only pose one possible weakness. For manufacturers, it is their R&D and its consequences which are the frequent causes of subsequent recalls. This calls for consistently incorporating the lessons learnt from past quality deficiencies along the entire product development chain: Which processes have causally not worked correctly? Where should the error have been detected before the customer became aware of it? This in particular allows for the deduction of process changes or improvements; if necessary, with interventions in structures and organisations, but also in matters concerning employee qualification.
Time as a significant factor in a real-case scenario
The greatest cost driver for recalls is usually the number of vehicles affected by the recall, whereby immediate error detection is an important factor. In this case, companies have to specifically invest in structures and mechanisms for the early detection and risk assessment of critical errors. Once errors have been identified, the actually affected production batches have to be investigated. Accurate isolation is a logistical and data-handling challenge. Especially when several suppliers are responsible for one component, vehicle-specific lot selection, which is therefore accepted by the Kraftfahrt-Bundesamt [German Federal Motor and Vehicle Transport Authority] is only possible if a data-compatible, precise allocation of the installed parts to the chassis numbers is provided.
Schließlich ist das Behördenmanagement für die Schadensbegrenzung wichtig. In the event of queries, all relevant data must be provided quickly if we are to establish trust. All things considered, honesty always pays off. After all, the past has shown that subsequently proven violations lead to severe penalty payments.
Kemény Boehme & Company
The mid-sized, internationally operating management consultancy Kemény Boehme & Company, founded in Munich in 2007, supports technology companies in optimising and efficiently structuring their complete bandwidth from development to procurement all the way to production. This is accomplished by Kemény Boehme & Company’s development of cross-sectoral, innovative solutions in active dialogue with network partners from technology centres and universities.