Project Example
Creating Transparency for Concept Issues and Purchased Parts Management in Plant Engineering
For a renowned plant engineering company, we developed and implemented a comprehensive concept to create transparency for ongoing concept issues and parts management.
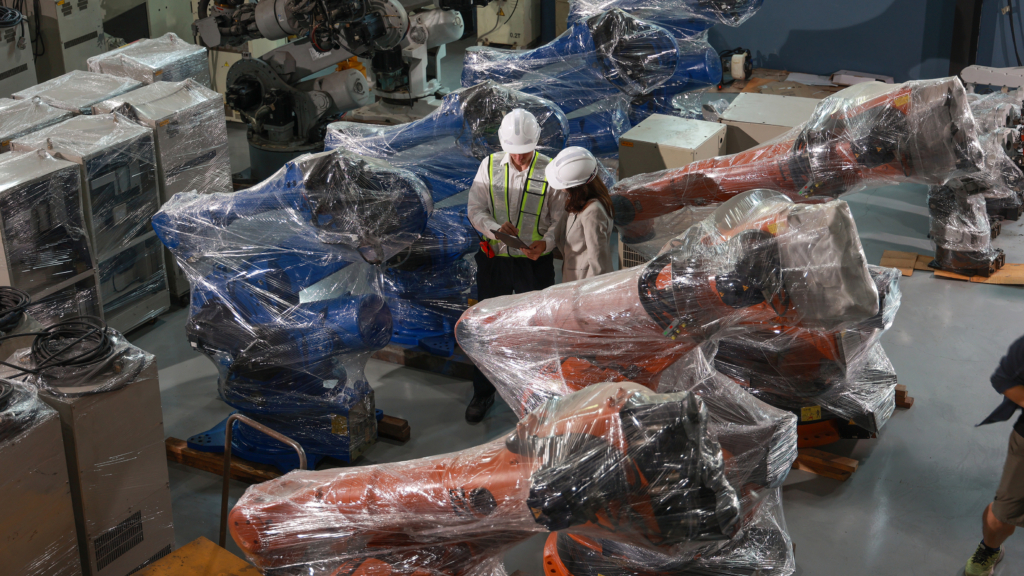
Background
The client was facing a lack of transparency regarding the processing status of ongoing concept issues and parts management. There was a lack of an overall overview and effective communication between different departments.
Specific Task
Our task included establishing a complete overview of the concept status, responsibilities, material status, delivery, assembly, and documentation. Additionally, we were to improve interface communication and initiate ad-hoc measures early when necessary.
KBC Solution Approach
We implemented daily reporting as a basis for quick management decisions. By introducing a joint daily fixed meeting, we efficiently clarified interface issues. We prioritized and managed more than 1,300 concept detail issues and established active parts management for in-house production as well as purchased parts.