Project Example
Stabilising suppliers in the case of bottlenecks in the supply chain
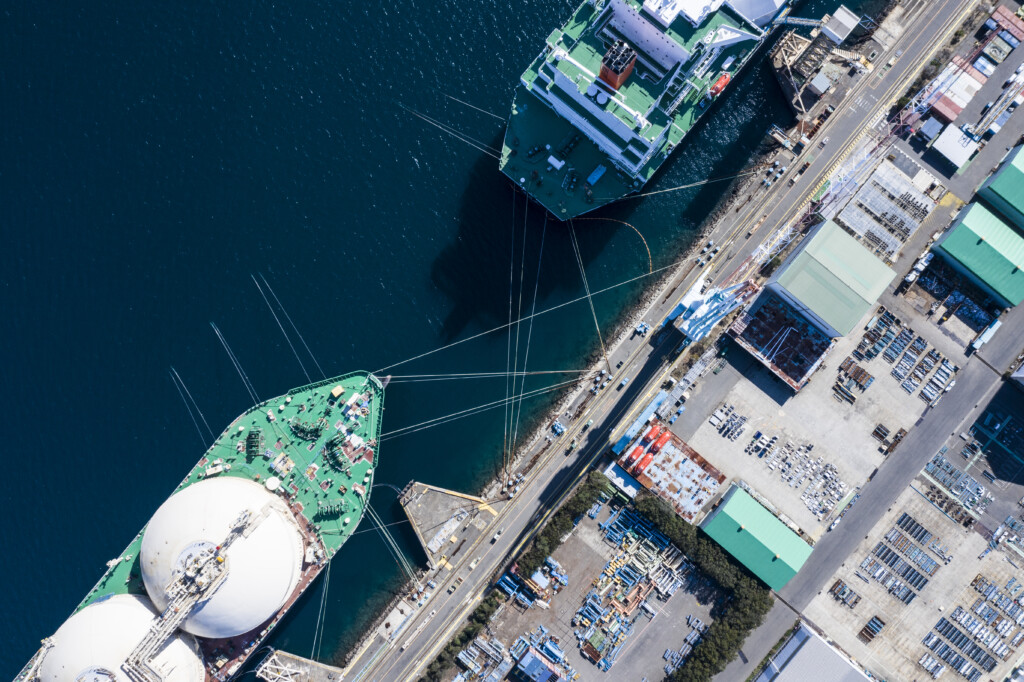
Background
The active management of larger supplier networks is becoming increasingly important and complex against the backdrop of sincreasing product quality requirements, more closely coordinated supply chains and a very dynamic economicn environments. This applies in particular to the automotive industry. The reliability of a supplier cannot be taken for granted in the first few years after its nomination. A holistic qualification before awarding and continuous audits after awarding counteract potential negative changes at the supplier and enable early detection of risks to one’s own supply chain. According to KBC’s experience, good supplier management is characterized not only by the rapid identification of weak points, but also by the active management of crisis situations that have already arisen.
Accordingly, short-term measures to stabilize suppliers are increasingly becoming the focus of many OEMs. The targeted deployment of interdisciplinary intervention teams (task force) can contain the effects of bottlenecks in the supply chain in the short term and eliminate weaknesses in the long term. Holistic transparency about supplier performance and stringent action management are essential.
Specific assignment
Restoring delivery capability and reducing the delivery backlog of a 1st tier supplier in the UK.
KBC approach
- Carrying out a root cause analysis to identify and prioritize the measures
- Introduction of key figures for the daily recording of the delivery performance of the 1st tier supplier
- Implementation of data-based sub-process analyses for quality assurance and reduction of reject rates
- Establishment of communication between OEM and suppliers and standardization of reporting up to the Management Board
- Daily Sdes task force-teams, prioritization and planning of parts deliveries and the solution of quality problems in the production chain
Realisation of potential
The OEM’s short and medium-term supply was successfully secured. Stringent reporting made performance transparent for the OEM at at Management Board level. Thanks to the regular exchange between the OEM, supplier and thetask force team, risks were identified as early as possible and escalation requirements were highlighted in good time. Targeted action tracking ensured a reduction in the reject rate of over 20% for central sub-processes. Supplier reliability as measured by OTIF (on-time in-full) was raised from below 10% to over 90%. A delivery backlog of ~ 3000 parts could be sustainably reduced through the close cooperation of suppliers and Taskforce-Team. In addition, several days’ worth of stock was built up in view of Brexit, which was imminent at the time.