Praxisbeispiel
Fehler vermeiden, Qualitätskosten reduzieren
Die Produktion eines führenden Automobil-OEMs optimierten wir in Richtung eines ambitionierten Ziels: „Null Fehler“.
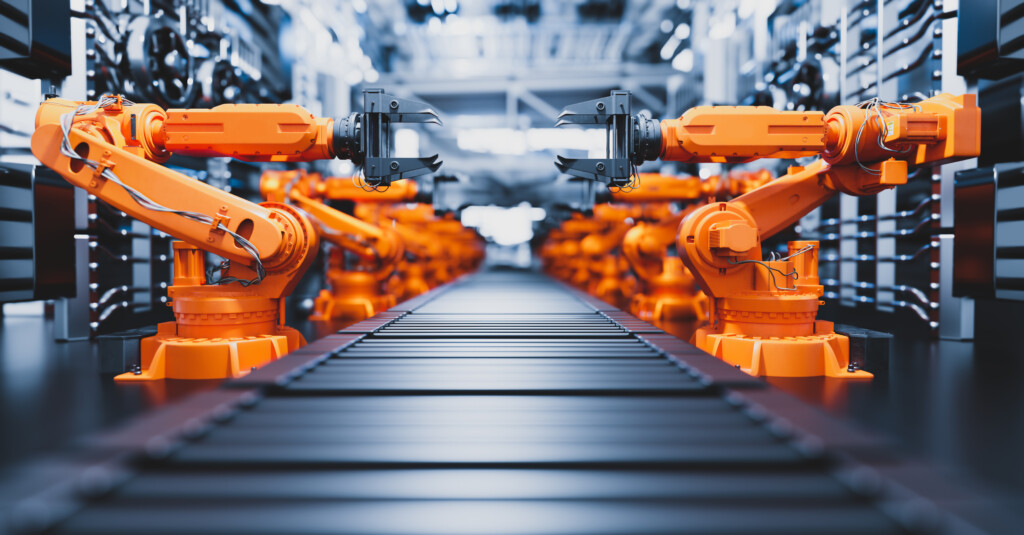
Hintergrund
Nach wie vor setzen Hersteller/OEMs ihren Fokus eher auf reaktive Maßnahmen nach Fehlerentstehung als auf präventive – obwohl Vermeidung und Prüfung die späteren Kosten der Fehlerbehebung reduzieren würden. Die Steuerung der Prozesse ist gut, aber die Prozessstabilität reicht trotzdem nicht aus. Kennzahlen sind vorhanden, aber das frühzeitige Erkennen und Vermeiden von Risiken ist nicht gewährleistet. Die Interpretation der Kennzahlen inkl. der Ableitung von Konsequenzen bleibt hinter dem Möglichen zurück. Gleichzeitig spielt auch die Geschwindigkeit in der Fehlerabstellung eine immer größere Rolle. Ein Umdenken ist deshalb gefragt: Fokus auf Prävention statt Reaktion. Es gilt zu handeln, bevor Fehler den Kunden erreichen.
Konkrete Aufgabenstellung
- Wirksamkeit des Null-Fehler-Programm in der Organisation erhöhen
- Konflikte bei der Priorisierung Programm vs. Linienfunktion lösen
- Reifegrad der Pilot-Maßnahmen für Roll-Out erhöhen
- Klare, regelmäßige Berichtsstruktur etablieren
- Prozess zur Mittelbeantragung vereinfachen und vereinheitlichen
- Ideenfindung zur Fehlervermeidung befeuern
KBC-Lösungsansatz
Zur Verortung von Fehlern in verursachenden Prozessen steuert KBC Präzision und Pragmatik bei. Wir sind fähig, die relevanten Optimierungsstellhebel mit weniger Kennzahlen abzudecken und eineindeutig zu verantworten. Unsere erprobte Methodik zur Business Case-Bewertung ermöglichte die richtige Maßnahmenpriorisierung und damit positive Wahrnehmung unseres Kunden bei den Schnittstellenpartnern und dem Vorstand.