Praxisbeispiel
Initialisierung, Umsetzung und Controlling einer Qualitätsinitiative zur Garantiekostenreduzierung
Aufbau der gesamten Steuerungs- und Controllingsprozesse im Rahmen einer Qualitätsinitiative bei einem führenden Premium-Automobilhersteller.
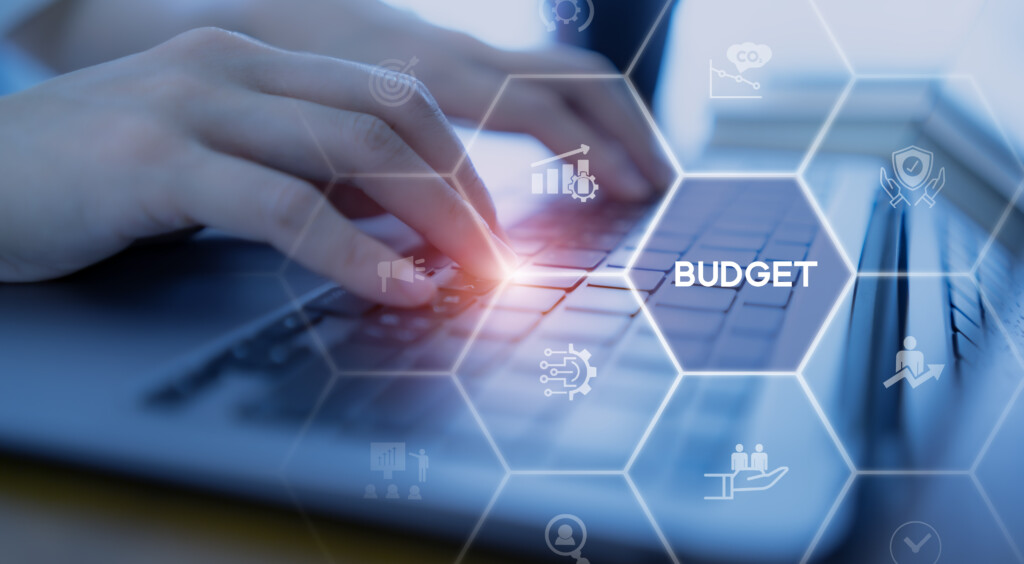
Hintergrund
Auswirkungen mangelhafter Produktzuverlässigkeit sind in der Automobilindustrie im Jahresabschluss der Gewinn- und Verlustrechnung (G&V) spürbar. Permanent steigende Gewährleistungs- und Kulanzkosten sind heutzutage der erste und spürbare Motivator bei der Initialisierung von Projekten zur Qualitäts- und Zuverlässigkeits-optimierung. Wesentlicher Faktor für den Erfolg solcher Optimierungsinitiativen ist die gleichzeitige und ausgewogene Umsetzung aus Produkt- und Prozessmaßnahmen. Kernherausforderung in der Gewährleistungskostenreduzierung ist dabei die Aufgabe der Strategie, die politischen und finanziellen Freiräume für solche Optimierungsprojekte zu schaffen. Für die Umsetzungsentscheidungen von Qualitätsmaßnahmen ist es daher zwingend erforderlich und auch möglich, den Nachweis der Rentabilität mittels Business Cases vor zu legen.
Konkrete Aufgabenstellung
- Maßnahmen zur Reduzierung der Gewährleistungskosten identifizieren
- Steuerungs- und Controllingprozesse (Programm und Umfeld) aufbauen
- Optimierungsmaßnahmen initialisieren und betriebswirtschaftlich bewerten (Aufwand und Nutzen)
KBC-Lösungsansatz
Neben der reinen Analyse und Identifizierung von Qualitätsmaßnahmen auf Basis von systematischen und bereichsübergreifenden Schwachstellenlandkarten konnten wir unserem Kunden unsere langjährige Erfahrung in der Initialisierung und im Controlling von großen Optimierungsinitiativen zur Seite stellen. Die inhaltliche Definition und Ausrichtung der Projekte sowie der Aufbau einer Berechnungssystematik zur monetären Nutzenquantifizierung von Qualitätsbefähigermaßnahmen auf Basis detaillierter Gewährleistungsdaten waren im ersten Schritt die wesentlichen Erfolgsfaktoren.
Darüber hinaus konnten wir gemeinsam mit unserem Kunden die Entscheidungsprozesse im Rahmen der Qualitätsorganisation, die in vielen Unternehmen Controlling getrieben sind, professionalisieren. Eine beschleunigte Maßnahmenumsetzung in Verbindung mit monetären Aussagen zum Nutzen, Aufwand sowie der Transparenz über Zielerreichung konnte nur durch die Installation eines Entscheidungsgremiums auf oberster Managementebene und der Einbindung aller funktionalen Bereiche erzielt werden.
Erzielte Wirkung
Durch die Initialisierung und konsequente Umsetzung der Qualitätsmaßnahmen auf Kundenseite konnte seit 2004 eine signifikante Reduzierung der Gewährleistungs- und Kulanzkosten (~50%) erreicht werden. Wir agieren dabei seit Jahren als rechte Hand für unseren Kunden und unterstützen in der Ausweitung dieses Erfolgsmodells durch die konsequente Anspannung der Zuverlässigkeitsziele.