Praxisbeispiel
Produktrückruf am Beispiel von Lithium-Ionen-Batterien
Ein Produktrückruf stellt Unternehmen, vor allem im Mittelstand, vor große Herausforderungen. Oftmals fehlt es den betroffenen Unternehmen an Erfahrung und den erforderlichen Kapazitäten. Dabei erfordern gerade Produktrückrufe ein kurzfristiges Handeln sowie eine schnelle Organisation der operativen Abwicklung.
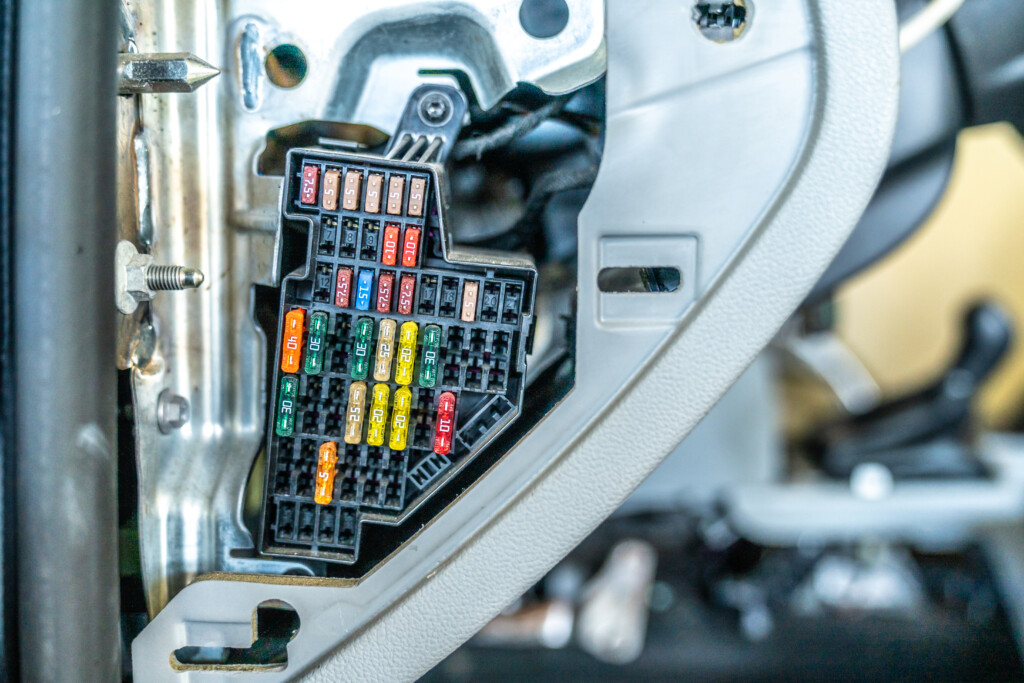
Hintergrund
Unser Kunde, ein Anbieter von eMobility Lösungen, entschied sich aufgrund seines hohen Qualitätsanspruches an die eigenen Produkte zur Durchführung einer freiwilligen, weltweiten Rückrufaktion für seine Lithium-Ionen-Batterien. Bei einem seiner Lieferanten lag eine Prozessschwäche in der Fertigung vor, die ein Risiko für die Produktsicherheit darstellte. Die besondere Herausforderung in diesem Fall lag neben einer sehr kurzen Vorbereitungszeit in der Größe (Kapazität) der Batterien. Für Lithium-Ionen-Batterien mit einer Kapazität größer 100 Wattstunden gelten hohe gesetzlichen Anforderungen in Hinblick auf Lagerung und Transport.
Konkrete Aufgabenstellung
Aufsetzen einer Rückrufaktion und Begleitung bis zum stabilen Regelbetrieb.
KBC-Lösungsansatz
Die Initialisierung der Rückrufaktion wurde in folgende Arbeitspakete gegliedert:
- Datenanalyse zur Eingrenzung der betroffenen Sachnummern und des pot. Rückrufvolumens
- Lieferantenmanagement zur Sicherstellung der Lieferfähigkeit
- Erstellung eines technischen Konzepts für den Test- und Reparaturprozess inkl. Servicedokumentation
- Definition und Implementierung der Serviceprozesse und -strukturen
- Erstellung eines Logistikkonzepts mit Pilotierung neuer Logistikpartner
- Globale Kommunikation an Behörden, Händler, Service Partner und Kunden über diverse Kanäle
Im Falle eines Rückrufs herrscht meist ein hoher Zeitdruck. Alle Aktivitäten müssen ineinandergreifen und entsprechend gut koordiniert werden. Eine detaillierte und umfassende Ablaufplanung zu Beginn bildet daher das Fundament einer erfolgreichen Rückrufaktion.
Zunächst sind die fehlerhaften Produkte am Markt einzugrenzen und das Rückrufvolumen abzuleiten. Hierfür wurden alle vorhandenen Daten von Lieferanten, Produktion und Verkauf ausgewertet. Eine gute Rückverfolgbarkeit von Produktionschargen ist ein wesentlicher Erfolgsfaktor, der Aufwand und Kosten reduziert.
Basierend auf dem Rückrufvolumen, muss die Verfügbarkeit von Ersatzteilen sichergestellt werden. Häufig stellt der kurzfristige Abruf großer Mengen auch die Lieferanten vor große Herausforderungen. Für unseren Kunden unterstützten wir deshalb zusätzlich zeitweise den Hauptlieferanten vor Ort. Zur Gewährleistung der dauerhaften Ersatzteilversorgung wurde ein enges Liefertracking aufgebaut.
Je nach Art des Produktes ist die Entwicklung eines durchdachten Test- u. Reparaturkonzeptes wichtig. Im vorliegenden Fall arbeiteten die Entwicklungs-, Qualitäts- und Serviceabteilung des Kunden eng zusammen, um ein Vorgehen zur Prüfung der Funktionalität und Sicherheit der Batterien zu erstellen. Aufgrund unserer technischen Expertise und langjährigen Erfahrung im Servicegeschäft konnten wir dem Kunden auch in technischen Fragestellungen beratend zur Seite stehen. Durch eine gute Servicedokumentation wurde der Aufwand für die Schulung von Servicepartnern reduziert. Mit Hilfe einer von uns entwickelten “Heat-Map” war man zusätzlich in der Lage, das Testequipment frühzeitig an die Servicepartner mit der höchsten Kundendichte zu verteilen.
Parallel zum technischen Vorgehen setzten wir gemeinsam mit dem Kunden ein Sonderprozess für den Service auf. Die Durchführung des Rückrufs brachte im Fall unseres Kunden eine starke Erhöhung der Serviceanfragen mit sich, weshalb die bestehende Organisation durch zusätzliche Mitarbeiter erweitert wurde. Hierfür ist eine detaillierte Planung der Abläufe essentiell, um eine Ressourcenabschätzung vornehmen zu können. Durch die Erstellung von Arbeitsanweisungen, Kommunikationsvorlagen und intensivem Coaching wurde das Serviceteam in der Anlaufphase durch KBC befähigt und zu Beginn des Produktrückrufs unterstützt. Dazu gehörte, neben der Definition der Prozesse, auch der Aufbau einer Toolunterstützung zur effizienten und durchgängigen Bearbeitung sowie zur Sicherstellung der Auswertbarkeit.
Für unseren Kunden war aufgrund hoher gesetzlicher Anforderungen vor allem der Transport der Batterien eine große Herausforderung. In enger Zusammenarbeit mit Logistikdienstleistern wurden hierfür länderspezifische Lösungen zur Abwicklung entwickelt und implementiert.
Den marktseitigen Startschuss für eine Rückrufaktion gibt die öffentliche Kommunikation. Mit Bekanntmachung sind alle betroffenen Kunden, Handelspartner und Behörden (konform mit den produktsicherheitsrechtlichen Anforderungen der jeweiligen Länder) zu informieren. In enger Abstimmung mit den Anwälten unseres Kunden wurde hierfür die entsprechende Kommunikation erstellt, die betroffenen Ansprechpartner identifiziert und eine weltweite Kommunikationskampagne über verschiede Kanäle durchgeführt.
Zur Steuerung der Rückrufaktion setzten wir ein regelmäßiges Reporting auf, das auch als Basis für Fortschrittsberichte an die Behörden erforderlich war. Nach der Initialisierung und der Anlaufunterstützung wurde die Steuerung der Rückrufaktion schrittweise an interne Mitarbeiter übergeben. Abschließend wurden präventive Maßnahmen definiert, um zukünftige Rückrufaktionen zu vermeiden. Hierfür wurde beispielsweise die Auswertung der End of Line-Prüfung beim Lieferanten automatisiert, um eine frühzeitige Identifizierung von Fehlerbildern sicherzustellen.