Praxisbeispiel
Modernes Problemmanagement für Prozesse
Wenn es langfristig gelingen soll, Produktprobleme nicht nur reaktiv sondern auch präventiv zu vermeiden, müssen systematisch die Schwachstellen in den wertschöpfenden und nicht-wertschöpfenden Prozessen optimiert werden. Mit unserer langjährigen Erfahrung im Bereich der Prozessoptimierung konzeptionieren wir gemeinsam mit unseren Kunden die zugehörigen Prozesse, Methoden und Tools und setzen die Ergebnisse bis zur Übergabe in die Linienfunktion um.
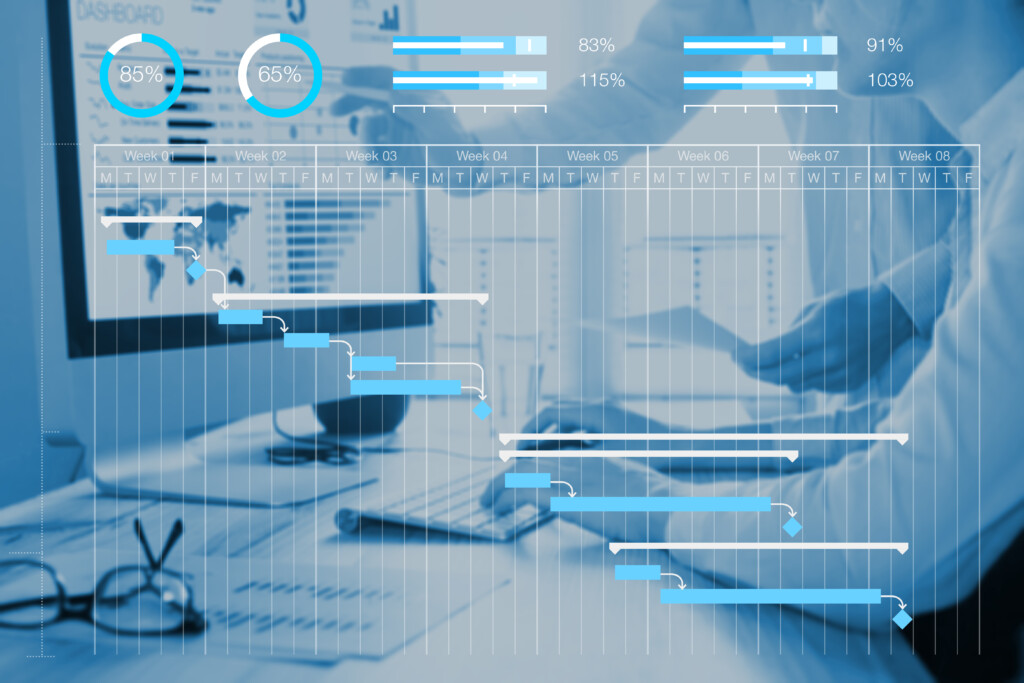
Hintergrund
Reaktives Problemmanagement ist für viele Unternehmen seit Jahren das Allheilmittel zur Reduzierung von Gewährleistungs- und Garantiekosten (Feldprobleme und Rückrufe). Die Produktprobleme werden jedoch nicht langfristig und insbesondere Produktgenerationen-übergreifend gelöst, da die wert- und nicht-wertschöpfenden Prozesse immer wieder die gleichen Fehler verursachen (z.B. Wiederholfehler). Die Ursachen für die Produktprobleme liegen jedoch in der mangelnden Optimierung der Prozesse, welche präventiv Fehler vermeiden könnten. Die Optimierung von unzureichenden Vorgehensweisen und der Aufbau von Methoden zur Ursachen- und Prozessanalyse sind somit die Kernherausforderungen, um von der Reaktion in die Prävention zu gelangen.
Konkrete Aufgabenstellung
- Konzeption und Umsetzung eines unternehmensweiten Prozesses und einer Methodik zur Ursachenanalyse (Generik) von Prozessproblemen bei auftretenden Produktproblemen.
- Aufbau von Steuerungs- und Analyseprozessen inklusive einer Toollandschaft (Excel).
- Aufbau und Umsetzung des zugehörigen Toolsets für den konzipierten Prozess und die Methode auf Basis Microsoft Excel (VBA).
- Umsetzung von spezifischen Reporting- und Auswertungsinstrumenten zur Steuerung der beteiligten Prozessschnittstellenpartnern und der Identifizierung von übergreifenden Handlungsbedarfen (Muster).
KBC-Lösungsansatz
Ausgehend von konkreten technischen Produktproblemen (z.B. Feldproblemen oder aus Rückrufen) lassen sich mit der Methodik zur Ursachenanalyse schnell, strukturiert und methodisch geführt die entsprechenden Prozessschwachstellen mit Hilfe der Ursachengenerik identifizieren. Aus den identifizierten Schwachstellen werden gezielt Prozessverbesserungsmaßnahmen abgeleitet und die Produktprobleme nachhaltig abgestellt.