Praxisbeispiel
Initialisierung einer Qualitätsoffensive zur Reduzierung der Qualitätsbezogenen Kosten
Analyse und Schaffung von Transparenz über die gesamten qualitätsbezogenen Kosten in den wertschöpfenden und nicht-wertschöpfenden Prozessen bei einem Hersteller in der medizintechnischen und pharmazeutischen Industrie.
Eine der wesentlichen Herausforderungen bei der Initialisierung von Qualitätsoffensiven, mit dem Ziel der Reduzierung der qualitätsbezogenen Kosten, ist die durchgängige Analyse der Prozessschwachstellen. Dafür ist eine Transparenz über die aktuelle Q-Kostensituation in den wertschöpfenden und nicht-wertschöpfenden Prozessen des jeweiligen Unternehmens unabdingbar.
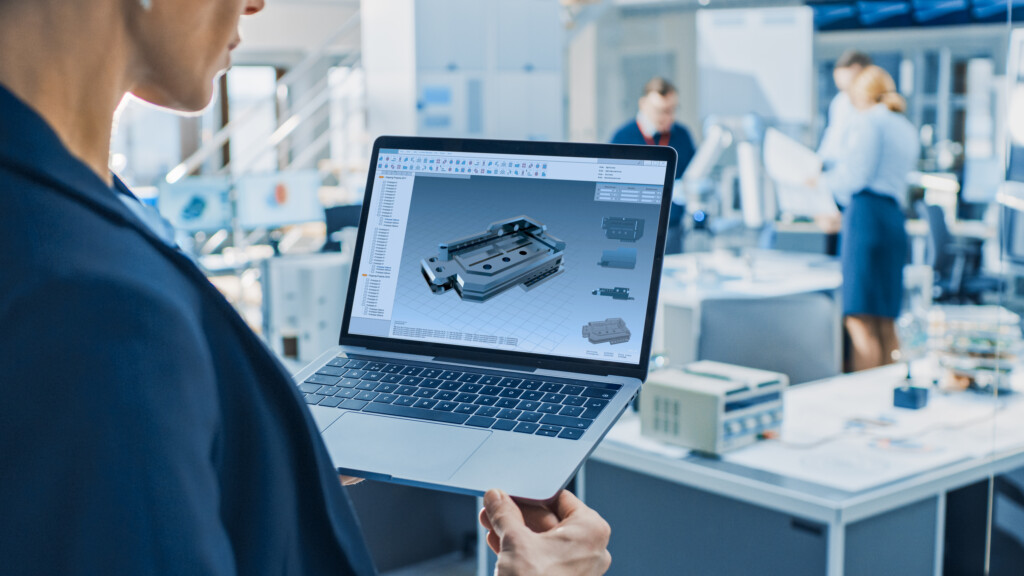
Hintergrund
- Steigende Kundenanforderungen und Qualitätsansprüche in den Märkten.
- Erhebliche Steigerung der Kosten für Non-Konformitäten (Reklamationskosten, Kulanzkosten).
- Fehlende Transparenz über die gesamten qualitätsbezogenen Kosten in den wertschöpfenden und nicht-wertschöpfenden Prozessen.
- Fehlender „Außenblick“ auf das Thema Qualität und Zuverlässigkeit (hinsichtlich Produkt und Prozess).
- Unzureichende Transparenz von Optimierungsbedarfen (Gesamtblick über Handlungsbedarfe inklusive Maßnahmenempfehlungen).
Konkrete Aufgabenstellung
- Schaffung von Transparenz für die qualitätsbezogenen Kosten.
- Unabhängige Bewertung des Qualitätsmanagements und der Q-relevanten Prozesse mittels „KBC Q-Scan“ (Top-down Q-Analyse).
- Identifikation von prozessualen Ursachen für ausgewählte Fehlerbilder von medizintechnischen Produkten (Rückverortung von Produktproblemen).
- Ableitung und Initialisierung von kurz-, mittel- und langfristigen Optimierungsempfehlungen.
KBC-Lösungsansatz
Bei der Durchführung des „KBC Q-Scans“ haben wir mit Hilfe eines strukturierten, interviewbasierten Fragebogens top-down die jeweiligen Prozessschwachstellen in den wertschöpfenden und nicht-wertschöpfenden Prozessen identifiziert.
Gleichzeitig konnten wir durch eine bottom-up durchgeführte Rückverortung bei konkreten technischen Produktproblemen mit Hilfe einer Ursachengenerik, die speziell auf unseren Kunden angepasst wurde, die entsprechenden Prozessschwachstellen schnell ermitteln. Diese Schwachstellen haben wir dann mit den Ergebnissen aus der Top-Down-Analyse abgeglichen, geclustert und priorisiert. Im nächsten Schritt wurden daraus gezielt Prozessverbesserungsmaßnahmen abgeleitet, mit dem Ziel die Produktprobleme nachhaltig abzustellen. Abschließend haben wir die empfohlenen Maßnahmen noch hinsichtlich ihrer Kosten und des potenziellen Nutzens für die qualitätsbezogenen Kosten in der Zukunft bewertet und die Ergebnisse für das Management transparent und Business-Case orientiert aufbereitet.