Project Example
Sustainable troubleshooting
In order to reach the quality targets in the production segment of a leading automotive OEM, we initialised a multi-plant zero-error programme.
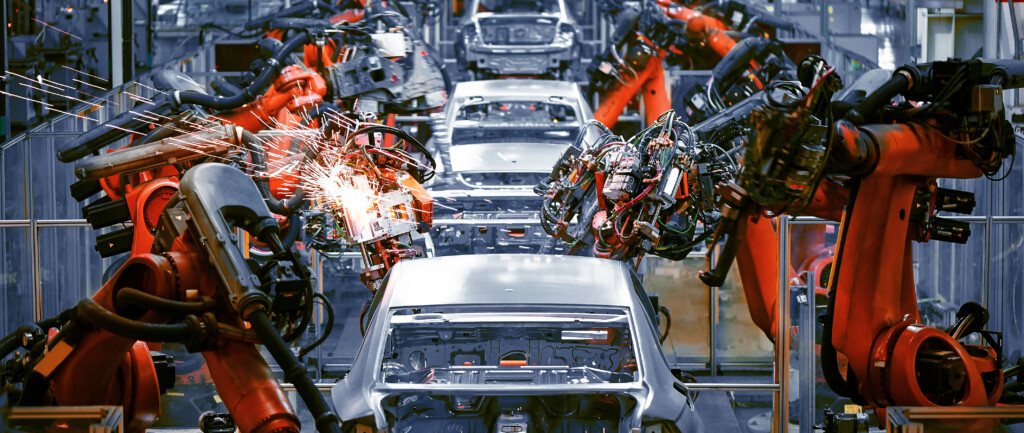
Background
Today’s economic environment poses numerous challenges for reliability management in the automotive industry. An increasing demand for the safety and reliability of end products is the consequence of equally increasing customer requirements. Complex processes, a large variety of products and shortened production times therefore also represent the major influencing factors of product quality in production. The automotive industry is faced with the task of reducing high quality costs while still achieving quality targets.
The specific task
- To reduce high quality costs in production
- To operationalise and harmonise previously determined directions of impact across multiple plants
- To develop concrete optimisation projects both contextually and economically
- To establish control models for the implementation of standards across multiple plants
KBC approach
During the development of a zero-error initiative in the production segment, we were able to support our client with our long-term experience in the initialisation of large optimisation initiatives. We acted as the right hand of our client’s programme management and, in project teamwork, controlled the contextual and economical alignment of the sub-projects across multiple plants. With an effect chain-based approach to the calculation of potentials of guarantee and warranty savings, we were quickly able to assess first monetary effects created by our optimisation measures. Active support from the individual plants during the initialisation of the sub-projects and from production management was therefore guaranteed from the start.