Project Example
Management of the supply chain in the case of a recall
The widely used modular systems in the automotive industry offer cost advantages in production and development on the one hand and also enable technically and qualitatively sophisticated products by reducing the number of variants. On the other hand, modular systems require a particularly high level of component protection, as conceptual and production-specific errors affect an even larger product population. Possible recalls can then become a nightmare for companies.
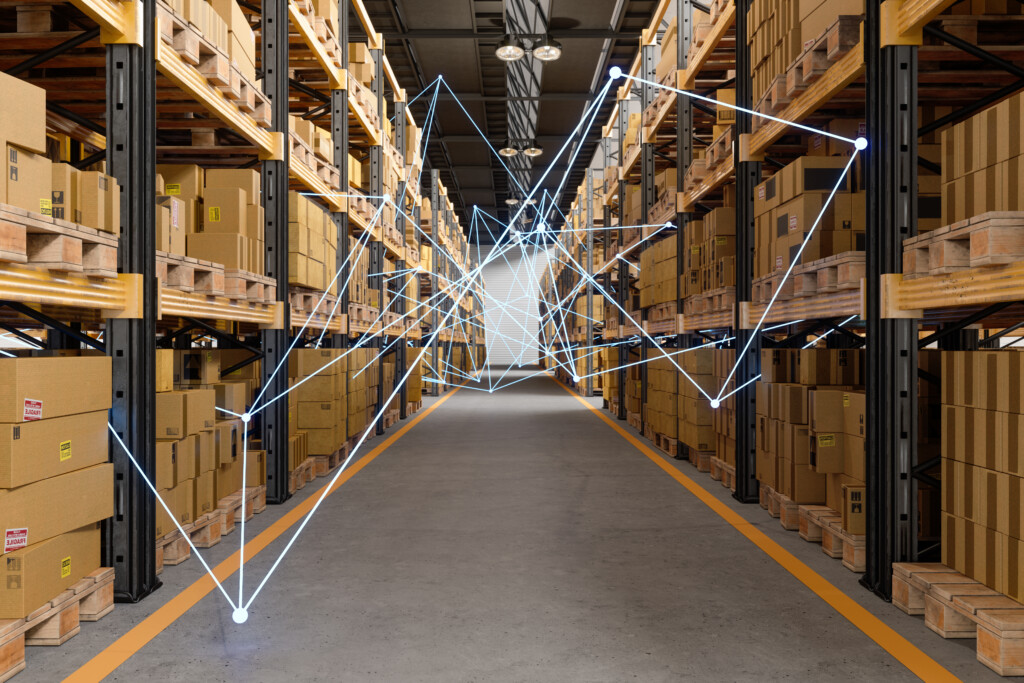
Background
Due to a conceptual error in a modular component, our customer, a car manufacturer, launched a worldwide recall of various engine variants and a large number of affected vehicles. The majority of the recalled components were no longer in series production at the supplier at this time. A lack of production capacity, long logistics routes and a complex variant structure made it difficult to meet the volatile demand for spare parts components on time. In addition, series production had to be maintained throughout the entire period.
Specific assignment
Demand management: Reliable forecast of component requirements by variant, location and time.
Production control: Demand-oriented control of the entire supply chain, taking into account available capacities, the variant mix, replacement flexibility and delivery times.
KBC approach
Demand management:
- Transparency about the risk population through the creation of a database of affected vehicles
- Transparency about the components installed in the vehicles, including of the production date
- Information on the current location of all vehicles and the repair status
- Forecasting customer behavior based on market-specific authority requirements and historical values
Production control:
- Transparency and tracking of subcontractor capacities and the availability of subcomponents
- Daily monitoring and control of production at the 1st tier supplier.
- Transparency of production capacities of individual lines and systems to identify bottleneck processes and potential for increasing capacity
- Control of delivery routes to bridge delivery bottlenecks
Achieved effect
A callback is a nerve-wracking affair for everyone involved, but especially for the customer. A smooth process is therefore crucial in order to minimize the annoyance of the customers affected. Long waiting times due to a lack of spare parts not only cause high costs in the short term (e.g.e.g. through the provision of replacement mobility), but also have a very negative impact on the company’s image in the long term.