Project Example
Indirect Spend Optimisation
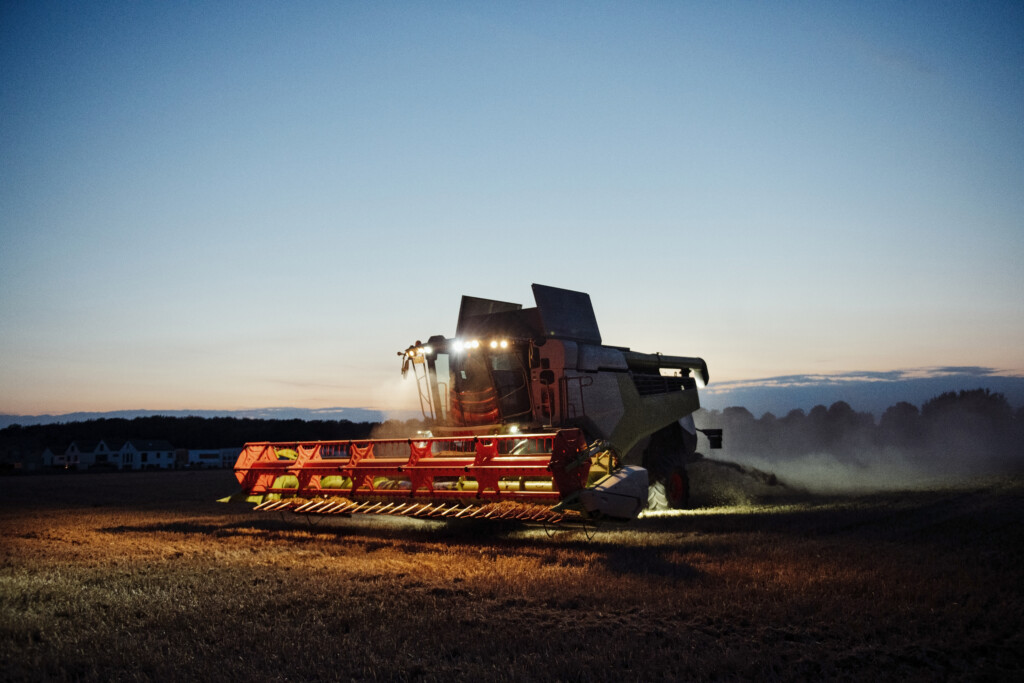
Background
An Operational Excellence Program aimed at securing and increasing profitability was set up at our customer, a manufacturer of commercial vehicles. One partial initiative of the program concerned the optimization of the (materials) overheads. The project approach originally chosen – to work purely with benchmarks – did not achieve the desired results and was discarded. Using a new approach, potential ways to close the gaps in the results had to be identified and discussed within three months.
The biggest challenge was joining a program with ambitious targets and a narrow timeframe that was already underway. An already highly-optimized cost basis and a high number of departments and stakeholders involved added to the difficulty.
Specific assignment
- Preparation and implementation of dialogues and workshops on costs, in direct and indirect areas to identify opportunities for savings
- Carrying out a cost analysis and evaluation of the savings opportunities identified
- Implementation of selected measures
- Consultation and agreement of the measures as well as regular reporting of the level of completion to top management and the board
KBC approach
The detailed analysis of cost drivers created a transparent basis for the methodical extrapolation of potential savings measures. As a result of the tight timeline, it was imperative that the preparation for the project was carried out systematically. As part of the verification and narrowing of the relevant costs in terms of both type and item, the individuals responsible for the budget and for costs in each case were identified and included in the project. The project approach was detailed and explained in-depth during dedicated workshops in order to ensure that the necessary project stakeholders and management were all “on board” from the beginning.
In the analysis phase,the drivers of volume for the (historical) cost development by type of costs were looked at. These formed the basis for the data and hypothesis-based development of savings measures.
The extrapolation of savings measures was carried out in the same manner for both the plant and for management functions:
- Standardized pre-analysis of costs
- Extrapolation of initial findings, in particular through a cross-departmental look at actual and planned costs.
- Dialogue using tools & volume drivers (KBC catalogue of measures)
- Extrapolation and prioritization of savings measures (ideas)
- Documentation and sign-off on the ideas generated as the basis for further evaluation
In the final project phase, the actions generated were evaluated and prioritized. Agreed measures were supported up to their implementation. The basis for this was specially defined overviews of the measures, including a financial evaluation and the description of the effects and potential risks.