Publication
Product recalls: The special case of high-voltage batteries in electric vehicles
Product recalls are unfortunately part of everyday business life – whether due to quality defects, safety concerns or legal violations. This is not a sector-specific phenomenon, on the contrary: they affect the automotive industry as well as mechanical and plant engineering, consumer electronics and the food industry. What all sectors have in common are the challenges, legal consequences, high costs and reputational damage that such a recall entails.
Reports of battery recalls for electric vehicles are currently piling up in the media. These are significantly more complex than conventional product recalls. In addition to the increased safety requirements for recalls, there are also special regulatory requirements for taking back and disposing of products. Companies must therefore establish a particularly careful and comprehensive recall management system to cover all aspects.
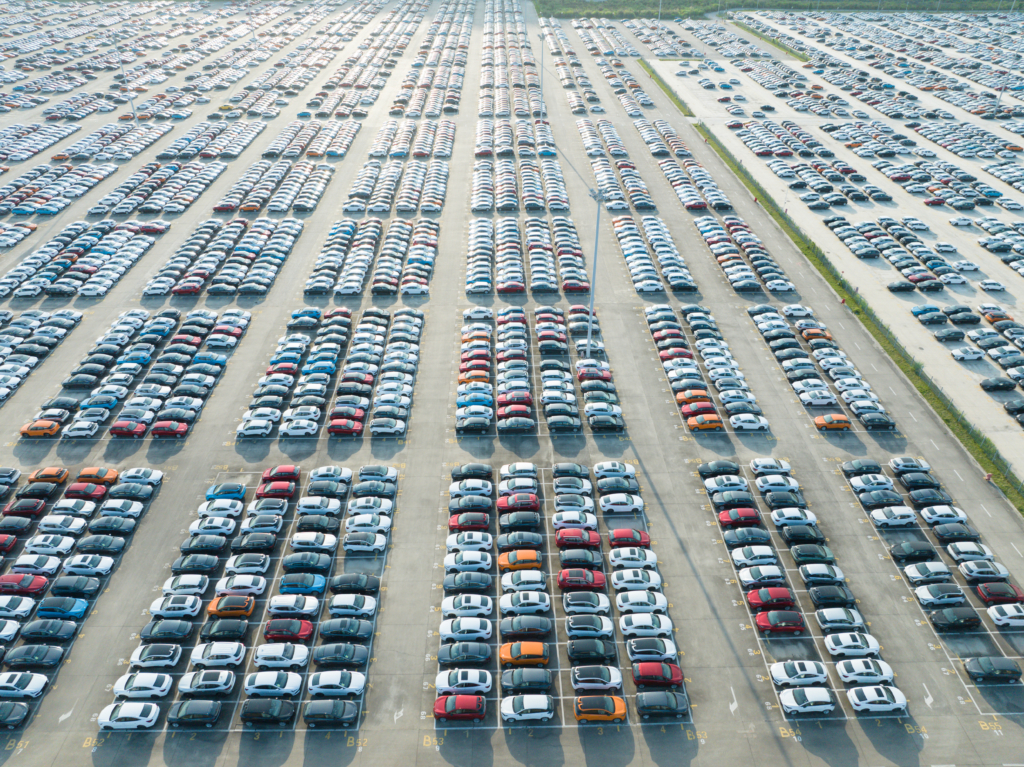
Preventing product recalls
To prevent this from happening in the first place, it is important to take preventive measures in advance to prevent product recalls as far as possible. It can be helpful here to establish the necessary roles, structures and processes that are required in the event of a recall. The error re-localization, i.e. tracing the causes back to the core processes forms the basis for sustainable measures to prevent errors for future product generations.
It is important to define standards in advance, according to which products are developed, manufactured and tested. In this way, technical causes of defects can be minimized right from the start. At the same time, there must be transparency in the supply chain so that problems can be identified at an early stage. Regular requalifications of suppliers can help to ensure the long-term accuracy and quality of components. A systematic analysis of field data is also crucial. By evaluating repair reports, customer complaints and other information from the market, critical product weaknesses can be identified before they lead to recalls.
Minimize the impact of recalls
If a recall is imminent, there are ways to mitigate the effects of a product recall. An important lever is the optimization of repair processes. Lean and efficient processing can significantly reduce the direct costs of retrieving, storing and disposing of the affected products. At the same time, adjusting parts prices can reduce purchasing costs.
In addition, it is useful to be able to estimate the scope of a potential recall at any time .Thanks to increased traceability and seamless monitoring of the supply chain, companies can determine exactly which products or batches are actually affected in order to quantify the potential recall quantity. At the same time, affected companies must ensure continuous communication with the authorities in order to minimize fines and other legal consequences.
Check product recalls
If the emergency has already occurred, it is important to manage the entire recall process in the best possible way. The systematic documentation of all measures and to create transparency of requirements, is essential. The following applies here: The more precisely the risk is assessed, the more detailed the quantity to be recalled can be determined. The so-called recall population is depending on the length of the supply chain and the depth of production. Once the affected customers have been identified, the geographical extent can be determined and the costs incurred can be estimated.
In order to meet the challenges of a recall efficiently, the performance of the suppliers, their production capacities and the repair status should be constantly monitored. On the one hand, in order to be able to exploit potential and, on the other, to recognize impending bottlenecks or failures at an early stage and initiate countermeasures. Because: security of supply for the recall campaign has top priority.
A successful recall campaign also requires a strategically well-planned, targeted communication campaign and returns management planned in detail. For affected customers, a recall is always associated with inconvenience, for which the manufacturer is held responsible. Therefore, Compensation and customer loyalty measures should be taken to counteract customer dissatisfaction and lasting damage to the company’s image.
Special case of battery recalls for electric vehicles
Battery recalls require significantly more complex and costly management than conventional product recalls. In addition to logistical challenges, particularly with defective or damaged high-voltage storage systems and regulatory requirements, their complexity is another aspect: high-voltage storage systems are highly integrated components whose development today focuses primarily on energy density and weight – and not on the replaceability of defective components. As the centerpiece and at the same time the most expensive component, up to 60 percent of the manufacturing costs are accounted for by the high-voltage batteries in electric vehicles. The common practice of scrapping these valuable components in the event of defects, damage or even a drop in performance is increasingly being criticized and drives up the costs of a product recall even further. If several model series or brands are also affected by the defect, a battery recall can cost billions.
A theoretical calculation example: The average manufacturing costs of an electric vehicle are currently approx. 32,000 €, with the battery included in this figure amounting to just under 16,000 € based on a conservative assumption of 50%. The most recent product recalls due to defects in the high-voltage battery amounted to up to 150,000 vehicles worldwide. If we assume that the storage system has to be replaced due to a significant defect or safety risk, the costs of this theoretical scenario for the high-voltage storage system alone amount to 2.4 billion €, the operational recall costs, costs for handling, installation and removal, recycling or repair of the defective storage units and any compensation from customers have not yet been taken into account.
Product recalls are an enormous challenge for companies and can be complex. It is therefore crucial to avoid recalls as far as possible and to take preventive action at an early stage. If the worst comes to the worst, the entire recall process must be precisely controlled, especially for electric vehicles with their highly complex and costly high-voltage batteries. In order to avoid extremely high costs in the event of battery recalls, manufacturers should focus even more strongly on the repairability of their storage systems in future. After all, the sustainability and economic viability of electromobility depends largely on the correct handling of defective high-voltage batteries.