Project Example
Ensuring Production Capability of a Power Supply Manufacturer through End-to-End Transparency
For a renowned manufacturer of power supply solutions, we optimized the supply chain to secure production capability and revenue targets. By creating end-to-end transparency from the end customer to the supplier, we were able to precisely capture material requirements and efficiently plan production.
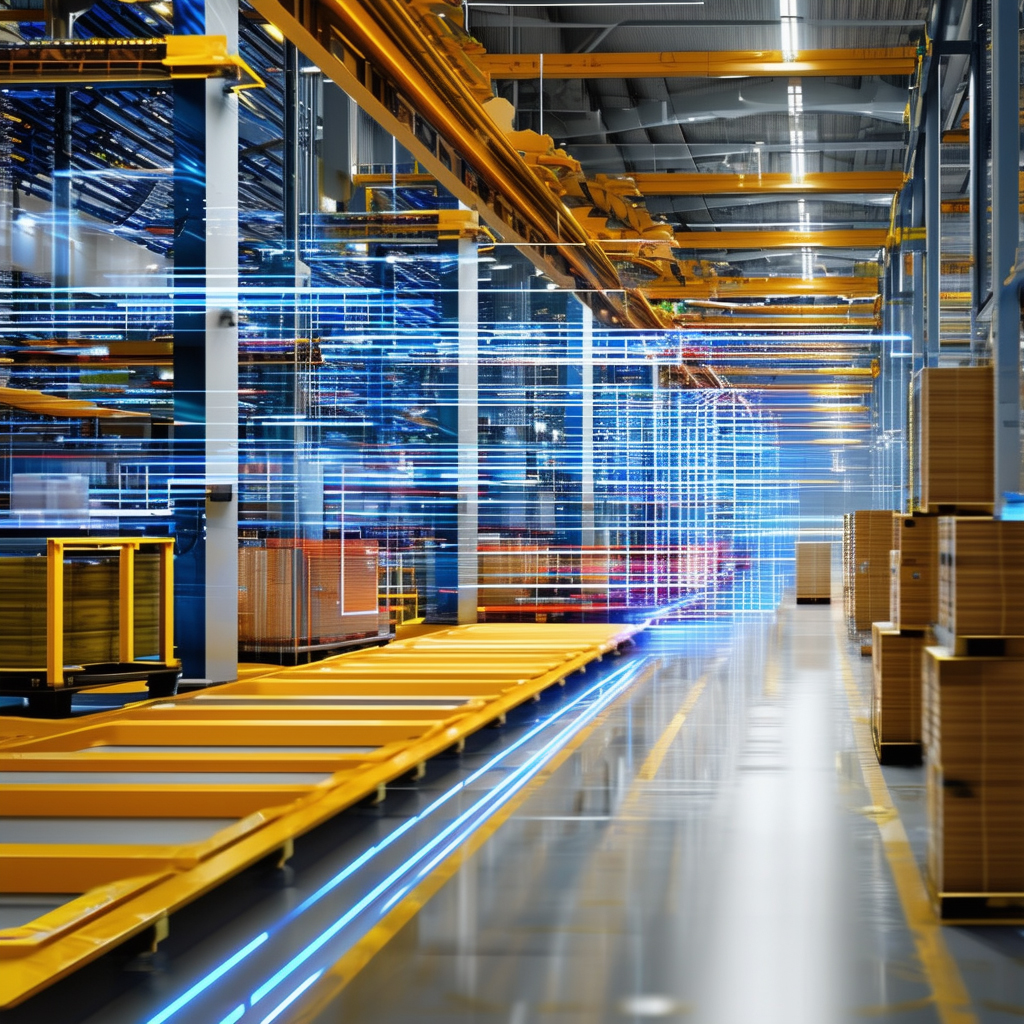
Background
The Covid-19 pandemic had led to a high backlog of customer orders as well as high material inventories. At the same time, production capability was limited by missing parts. There was a lack of transparency in the ERP system to assess production possibilities and procurement necessities.
Specific Task
Our task was to create complete transparency of material requirements, simulate production scenarios, and systematically identify missing parts. The goal was to automate knowledge about relationships between customer orders, bills of materials, and alternative components, and to optimize production planning.
KBC Solution Approach
We developed a data model to simulate production scenarios and optimize inventories. By analyzing master and transaction data in the ERP system, we generated knowledge from relationships between sales, purchasing, logistics, and production data. We evaluated all missing parts regarding their criticality for components and suppliers and established targeted working capital management.