Project Example
Optimization of Flow Production at an Agricultural Machinery Manufacturer
For a leading agricultural machinery manufacturer, we optimized the flow production of complex products with high variance. Our goal was to sustainably increase the first-pass yield and manufacturing quality, as well as improve the supply situation on the production line.
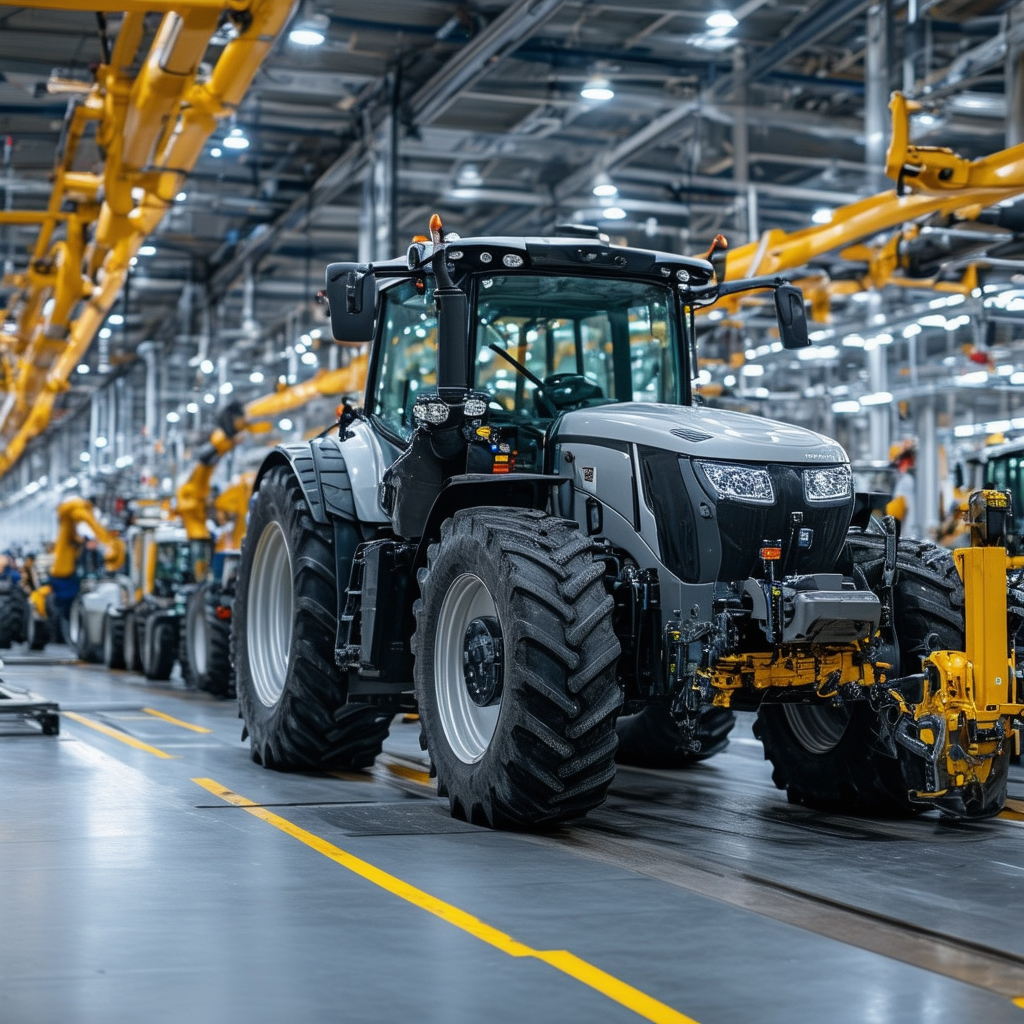
Background
The client operates a flow production for very complex products in various versions with a batch size of 1. Challenges included missing parts, supply bottlenecks, and above-average rework efforts.
Specific Task
Our task was to analyze existing data from ERP and MES systems to create transparency and recognize patterns in error profiles. We conducted detailed root cause analyses and derived optimization measures based on lean production principles.
KBC Solution Approach
We applied established quality methods such as fault tree analysis, Ishikawa diagram, and 5-Why analysis. Problem-solving teams were formed, and the implementation of sustainable solutions was supported. By creating transparency regarding the missing parts and supply situation, we were able to effect targeted improvements.