Project Example
Optimisation of a quality assurance organisation in the mobility industry
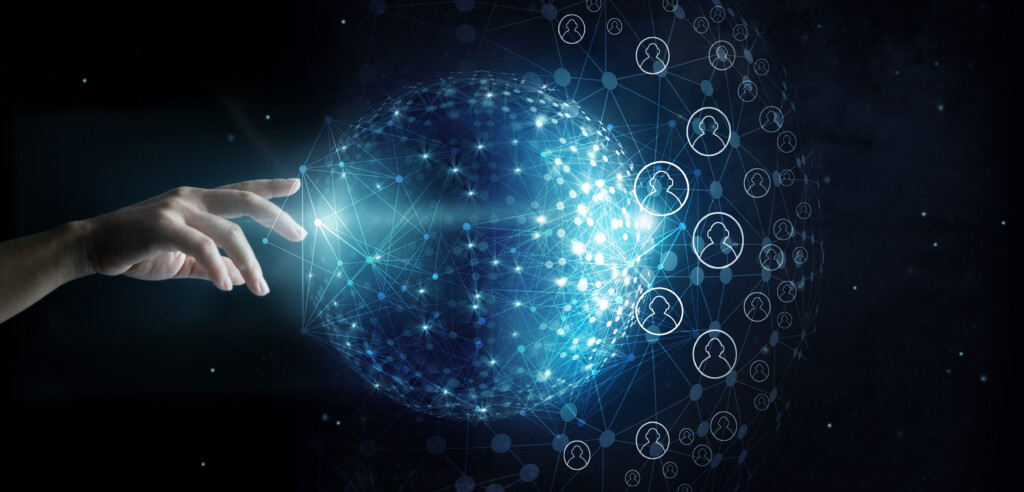
Background
Companies in the mobility industry often have organisational structures that have simply evolved, leading to the structure standing in the way of products and services of excellent quality assurance. Examples of this are, among others:
- An entirely decentralised quality assurance organisation, with different Q-standards and quality levels across different production locations.
- A quality assurance organisation that must act as the customer’s advocate for the quality of the products or services without a mandate.
In this respect, the question of the “correct or the best” organisational form frequently comes up.
Based on our long years of project experience in the quality arena, there is no sweeping answer to this question. Actually, it can almost only be answered in connection with the specific needs in each individual case. Unfortunately, as is so often the case: “it depends”.
For us, various issues with regard to the quality assurance work in question are relevant in order to be able to work out improvement measures little by little:
- Is the current QA organisation organised centrally or decentralised?
- To what extent and how well does the quality assurance work take place in the value adding steps (e.g. development, production) for each product or service?
- Does the QA organisation work with a focus on preventative or reactive measures?
- How high are my costs for preventative and reactive quality work?
- What feedback do I have from customers regarding the quality of my products or services?
- How well is the quality assurance organisation’s mandate accepted in the company, how pronounced is it and how much is it already lived?
- How independently can the QA organisation operate in comparison to the value-adding areas?
Specific assignment
After assessing and analysing individual customer situations, again and again we come across similar challenges in our customer projects to optimise quality assurance organisations:
- No explicitly identified or lived QA roles
- No clear mandate to prioritise quality assurance tasks
- A lack of central steering of quality assurance measures or improvements
- A lack of action tracking and weak implementation of quality measures
Depending on the situation various optimisation measures are drawn up.
KBC approach
In one customer project in the mobility industry, the underlying quality process analysis for the identification of process deficits in quality assurance activities was the key to success. One finding was that the core quality processes in the company were not clearly described and so were not being lived. In our customer project, the process analysis also helped, through the transparency that arose as a result, to initiate the right quality optimisation measures in the right places while at the same time not overwhelming the existing quality assurance organisation.
An additional crucial element for success was the establishment of a quality assurance organisation with centralised and decentralised portions building on structures that already existed. In this regard, in order to establish a holistic and interrelated quality network in the company, we also paid attention to taking the relevant quality departments into consideration in the operative value-added areas. This network serves as the foundation and the basis of future quality work for further optimisations in all of our customer’s significant quality processes.