Project Example
Interim Management to Stabilize Production of a Foundry After Insolvency
Following a long insolvency phase and a change in ownership, a medium-sized foundry faced significant organizational, procedural, and technological challenges. High delivery backlogs due to low Overall Equipment Effectiveness (OEE) and outdated machinery urgently required rapid stabilization of business operations.
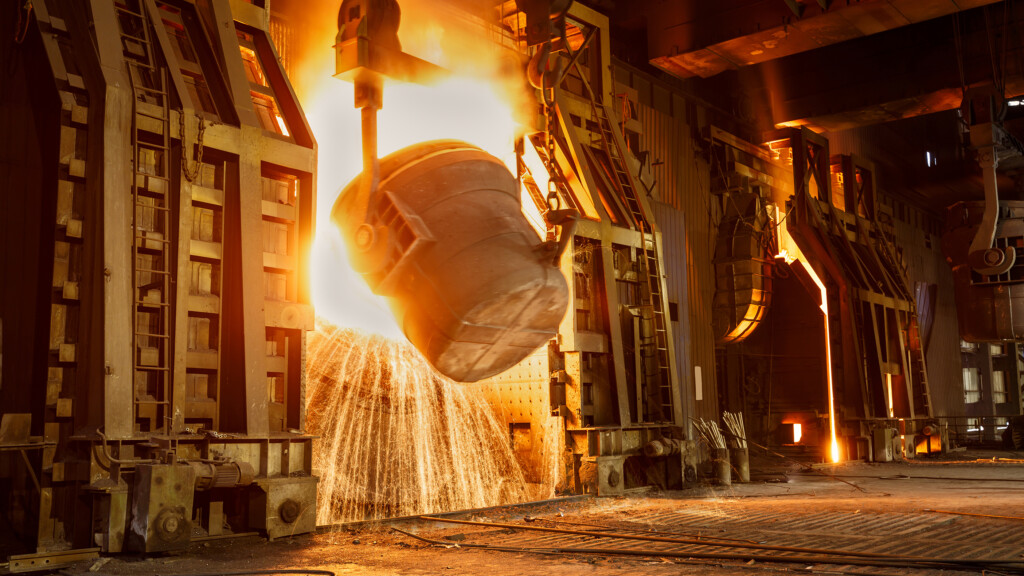
Background
The foundry suffered from inadequate analog data collection and lack of optimization processes across the entire production. This led to considerable inefficiencies and losses in machines, tools, and fixtures. A comprehensive restructuring of production was urgently needed to stabilize business operations and restore competitiveness.
Specific Task
Our task was to immediately create transparency regarding plant data, production figures, and types of OEE losses. Based on this, the OEE was to be increased by reducing organizational, technical, and qualitative losses. At the same time, we were to increase efficiency in production control and production processes to reduce delivery backlogs and sustainably stabilize business operations.
KBC Solution Approach
We first established systematic collection and analysis of production data to create transparency about occurring types of losses and inefficiencies. Using this data, we prioritized action needs and derived fact-based optimization activities. Through targeted measures, we increased plant availability and efficiency in production control and processes. A special focus was on reducing technical, organizational, and qualitative production time losses to significantly increase OEE.